تولید لوله فولادی به عنوان یکی از مهمترین بخشهای صنعت فولاد، نقشی اساسی در زیرساختهای صنعتی و عمرانی جهان ایفا میکند. از خطوط انتقال نفت و گاز گرفته تا ساخت و ساز و صنایع پتروشیمی، این لولهها به دلیل استحکام و مقاومت بالای خود، جایگاهی غیرقابلانکار دارند. بر اساس گزارشهای انجمن جهانی فولاد (World Steel Association)، تولید لولههای فولادی بیش از 15 درصد از کل مصرف فولاد جهان را تشکیل میدهد که نشاندهنده اهمیت استراتژیک آن در اقتصاد جهانی است. فرآیند تولید این لولهها شامل مراحل پیچیدهای همچون نورد گرم، نورد سرد و جوشکاری است که با بهرهگیری از فناوریهای پیشرفته، محصولاتی با کیفیت و کارایی بالا عرضه میکند. در این مقاله، با بررسی جامع فرآیند تولید، انواع مختلف لولههای فولادی و کاربردهای متنوع آنها، شما را دعوت میکنیم تا اطلاعات بیشتری کسب کرده و با دنیای پرپیچ و خم این صنعت استراتژیک آشنا شوید. همراه ما باشید!
مواد اولیه تولید لوله فولادی؛ از سنگ آهن تا فولاد خالص
تولید لوله فولادی با انتخاب دقیق مواد اولیه آغاز میشود. سنگ آهن به عنوان ماده اصلی، پس از استخراج وارد مرحله احیای مستقیم میشود که طی آن به آهن خالص تبدیل میگردد. سپس با افزودن عناصر آلیاژی نظیر کروم، نیکل و مولیبدن، ترکیبات مختلفی از فولاد به دست میآید که هر کدام ویژگیهای خاصی دارند. برای مثال، افزودن کروم باعث افزایش مقاومت در برابر خوردگی میشود که در تولید لولههای نفت و گاز بسیار اهمیت دارد. خط تولید لوله با توجه به نوع کاربرد، از فولاد کربنی، فولاد ضدزنگ و یا فولاد آلیاژی استفاده میکند. طبق گزارشهای انجمن فولاد اروپا (Eurofer)، استفاده از فولادهای آلیاژی در تولید لولههای صنعتی به طور متوسط 30 درصد بهرهوری انرژی را افزایش میدهد. انتخاب صحیح مواد اولیه و ترکیبات آلیاژی، نه تنها کیفیت نهایی محصول را تضمین میکند بلکه به کاهش هزینههای نگهداری و افزایش عمر مفید لولهها کمک میکند.
فرآیند تولید لوله فولادی؛ از نورد گرم تا جوشکاری مدرن
فرآیند تولید لوله فولادی شامل مراحل متعددی از نورد گرم و نورد سرد گرفته تا جوشکاری پیشرفته است. مجتمع تخصصی صنعتی کاجاران به عنوان یکی از پیشروان این صنعت، با بهرهگیری از فناوریهای روز دنیا، محصولات با کیفیتی را عرضه میکند. نورد گرم، اولین مرحله تولید است که در آن ورقهای فولادی تحت دما و فشار بالا به شکل لوله در میآیند. سپس در فرآیند نورد سرد، سطح لوله صیقل داده شده و خواص مکانیکی آن بهبود مییابد. جوشکاری نیز به روشهای مختلفی چون جوشکاری مقاومت الکتریکی (ERW) و جوشکاری زیرپودری (SAW) انجام میشود. بر اساس تحقیقات انجامشده توسط مؤسسه ملی جوش آمریکا (AWS)، استفاده از روشهای مدرن جوشکاری میتواند تا 40 درصد استحکام لولههای فولادی را افزایش دهد. انتخاب صحیح روشهای نورد و جوشکاری، تضمینکننده کیفیت و کارایی لولههای فولادی در شرایط مختلف است.
کنترل کیفیت در تولید لوله فولادی؛ استانداردها و آزمایشهای ضروری
تولید لوله فولادی نیازمند رعایت استانداردهای سختگیرانهای است که شامل آزمایشهای مکانیکی، شیمیایی و غیرمخرب میشود. خط تولید لوله پی وی سی به دلیل استفاده گسترده در انتقال سیالات، نیازمند کنترل کیفیت دقیقتری است. استانداردهای بینالمللی نظیر ASTM و API، حداقل الزامات را برای تضمین کیفیت لولههای فولادی تعیین میکنند. آزمایشهای مکانیکی شامل تستهای کشش، فشار و خمش است که مقاومت لوله را در برابر شرایط سخت بررسی میکند. همچنین، آزمایشهای شیمیایی با تحلیل ترکیب آلیاژها، میزان عناصر مضر نظیر گوگرد و فسفر را کنترل میکنند. بهکارگیری تجهیزات پیشرفتهای چون دستگاههای اولتراسونیک و رادیوگرافی برای تشخیص عیوب داخلی، بخش دیگری از فرآیند کنترل کیفیت است. رعایت این استانداردها نه تنها به بهبود عملکرد لولههای فولادی کمک میکند بلکه از هزینههای اضافی ناشی از تعمیرات و تعویضهای مکرر جلوگیری میکند.
پوششدهی و حفاظت لولههای فولادی؛ روشهای مقاومسازی در برابر خوردگی
تولید لوله فولادی نیازمند پوششدهیهای مقاوم به خوردگی است تا در محیطهای اسیدی، نمکی و مرطوب دوام بیشتری داشته باشد. خط تولید لوله پلیپروپیلن به دلیل مزایای آن در مقاومت شیمیایی، به یکی از پرطرفدارترین گزینهها تبدیل شده است. روشهای پوششدهی شامل گالوانیزه گرم، اپوکسی و پلیاتیلن است که هرکدام ویژگیهای خاصی دارند. طبق مطالعات انجمن حفاظت از خوردگی آمریکا (NACE)، استفاده از پوششهای پلیاتیلن میتواند تا 50 درصد عمر مفید لولههای فولادی را افزایش دهد. پوششهای اپوکسی به دلیل چسبندگی بالا و مقاومت در برابر مواد شیمیایی، بیشتر در خطوط انتقال نفت و گاز به کار میروند. انتخاب پوشش مناسب، نه تنها هزینههای نگهداری را کاهش میدهد بلکه ایمنی و پایداری سیستمهای انتقال را تضمین میکند. رعایت استانداردهای پوششدهی میتواند نقش مهمی در جلوگیری از خرابیهای زودرس و کاهش هزینههای تعمیرات ایفا کند.
لولههای فولادی بدون درز و درزدار؛ تفاوتها و کاربردهای هر کدام
تولید لوله فولادی به دو روش اصلی بدون درز (Seamless) و درزدار (ERW) انجام میشود که هر یک ویژگیها و کاربردهای خاص خود را دارند. لولههای بدون درز، از طریق نورد و کشش یکپارچه و بدون جوش تولید میشوند که به دلیل نبود درز، دارای استحکام و تحمل فشار بالاتری هستند. این نوع لولهها بیشتر در صنایع نفت و گاز و جایی که انتقال سیالات تحت فشار بالا مطرح است، استفاده میشوند. از سوی دیگر، لولههای درزدار با استفاده از ورقهای فولادی و جوشکاری مقاومتی تولید میشوند که هزینه تولید کمتری دارند و در کاربردهای کمفشار مانند ساخت سازههای فلزی و سیستمهای تهویه مورد استفاده قرار میگیرند. طبق گزارش مؤسسه تحقیقات بازار (Market Research Future)، تقاضا برای لولههای بدون درز به دلیل نیاز به ایمنی بیشتر در صنایع نفت و گاز، سالانه 6 درصد رشد داشته است. انتخاب بین این دو نوع لوله باید با توجه به نوع کاربری، فشار و شرایط محیطی صورت گیرد.
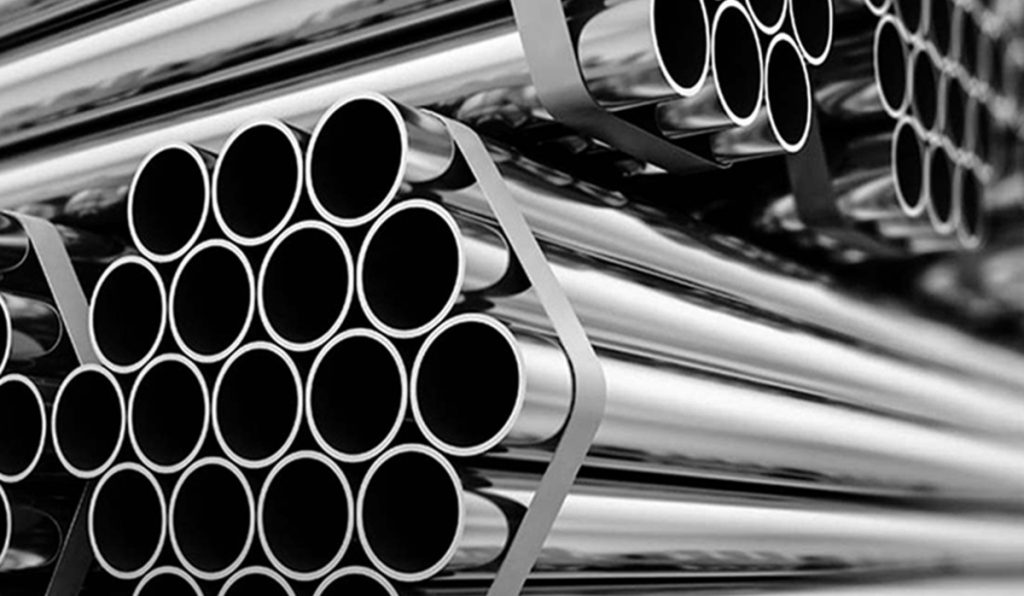
کاربردهای متنوع لولههای فولادی؛ از انتقال سیالات تا سازههای صنعتی
تولید لوله فولادی به دلیل ویژگیهای منحصر به فرد نظیر استحکام، مقاومت به خوردگی و قابلیت تولید در ابعاد مختلف، کاربردهای گستردهای در صنایع مختلف دارد. در صنعت نفت و گاز، این لولهها برای انتقال سیالات تحت فشار بالا و در محیطهای خورنده به کار میروند. در صنعت ساخت و ساز، لولههای فولادی به عنوان ستونهای پشتیبان و سیستمهای انتقال آب و فاضلاب مورد استفاده قرار میگیرند. همچنین، در صنایع شیمیایی و پتروشیمی، این لولهها به دلیل مقاومت بالا در برابر مواد شیمیایی، نقش کلیدی ایفا میکنند. طبق گزارش انجمن جهانی فولاد، بیش از 30 درصد لولههای تولید شده در جهان، در صنایع انرژی مورد استفاده قرار میگیرند. انتخاب صحیح لوله فولادی با توجه به شرایط محیطی و نوع سیال میتواند به افزایش طول عمر و کاهش هزینههای تعمیرات و نگهداری کمک کند.
پایدارسازی و بازیافت لولههای فولادی؛ گامی به سوی توسعه پایدار
تولید لوله فولادی نه تنها باید بهینه و اقتصادی باشد، بلکه از منظر زیستمحیطی نیز باید مورد توجه قرار گیرد. بازیافت لولههای فولادی به دلیل قابلیت بازیافت 100 درصدی، یکی از راهکارهای مؤثر در کاهش ضایعات صنعتی و حفظ منابع طبیعی است. فرآیند بازیافت شامل ذوب مجدد لولههای قدیمی و تولید محصولات جدید میشود که در کاهش مصرف انرژی و انتشار گازهای گلخانهای نقش مهمی دارد. بر اساس تحقیقات مؤسسه بینالمللی بازیافت (BIR)، بازیافت فولاد میتواند تا 60 درصد انرژی کمتری نسبت به تولید فولاد از سنگ آهن مصرف کند. همچنین، استفاده از فناوریهای نوین مانند پوششهای نانویی و حفاظت کاتدی میتواند به افزایش طول عمر لولههای فولادی کمک کند. این اقدامات نه تنها به کاهش هزینههای تعمیر و نگهداری میانجامد بلکه به توسعه پایدار و حفظ محیط زیست نیز کمک میکند.
چالشهای تولید لوله فولادی در ایران؛ موانع و راهکارهای علمی
تولید لوله فولادی در ایران با چالشهای متعددی از جمله کمبود مواد اولیه، تحریمهای اقتصادی و فناوریهای قدیمی مواجه است. وابستگی به واردات ورقهای فولادی و تجهیزات پیشرفته باعث افزایش هزینههای تولید و کاهش رقابتپذیری محصولات ایرانی در بازارهای جهانی شده است. علاوه بر این، محدودیتهای انرژی و قوانین سختگیرانه محیطزیستی، مشکلاتی دیگر برای تولیدکنندگان ایجاد کرده است. طبق آمار انجمن تولیدکنندگان فولاد ایران، ظرفیت تولید لولههای فولادی در کشور تنها 70 درصد از ظرفیت واقعی است. راهکارهای علمی برای حل این چالشها شامل بومیسازی فناوریهای تولید، استفاده از مواد اولیه داخلی و ارتقاء سطح دانش فنی کارکنان میشود. همچنین، سرمایهگذاری در تحقیق و توسعه (R&D) میتواند به بهبود فرآیندهای تولید و کاهش وابستگی به تکنولوژیهای خارجی کمک کند.
آینده تولید لولههای فولادی؛ روندها و فناوریهای نوظهور
تولید لوله فولادی به سوی استفاده از فناوریهای نوین مانند لولههای هوشمند و اینترنت اشیاء (IoT) در حال حرکت است. لولههای هوشمند با سنسورهای داخلی قادرند پارامترهایی نظیر فشار، دما و خوردگی را به صورت لحظهای مانیتور کنند و اطلاعات آن را به مراکز کنترل ارسال نمایند. این فناوری میتواند هزینههای تعمیرات را تا 30 درصد کاهش دهد. همچنین، استفاده از روباتها در بازرسیهای داخلی لولهها، سرعت و دقت این فرآیند را به طور چشمگیری افزایش داده است. بر اساس گزارش موسسه تحقیقاتی Grand View Research، بازار لولههای هوشمند تا سال 2030 با نرخ رشد سالانه 8 درصد، به ارزش 9 میلیارد دلار خواهد رسید. علاوه بر این، توسعه فناوریهای پوششدهی نانویی و استفاده از آلیاژهای جدید با مقاومت بالاتر میتواند طول عمر لولههای فولادی را به طور قابل توجهی افزایش دهد. آینده تولید لولههای فولادی، با تمرکز بر بهینهسازی مصرف انرژی و کاهش اثرات زیستمحیطی، به سمت پایداری و هوشمندسازی پیش میرود.
انتخاب بهترین لوله فولادی؛ نکات کلیدی و توصیههای تخصصی
تولید لوله فولادی با توجه به گستردگی کاربردها و تنوع محصولات، نیازمند دانش فنی و آگاهی دقیق از استانداردها و تکنولوژیهای مدرن است. انتخاب صحیح لوله فولادی باید با در نظر گرفتن عوامل متعددی چون نوع سیال، فشار، دما و شرایط محیطی انجام شود. همچنین، رعایت استانداردهای بینالمللی مانند API و ASTM میتواند کیفیت و ایمنی لولهها را تضمین کند. استفاده از پوششهای مقاوم به خوردگی و توجه به فرآیندهای بازیافت و پایداری، از دیگر عواملی است که در انتخاب لولههای فولادی باید مد نظر قرار گیرد. در نهایت، بهرهگیری از فناوریهای نوین مانند لولههای هوشمند و سیستمهای مانیتورینگ، میتواند هزینههای نگهداری را به طور قابل توجهی کاهش داده و عمر مفید سیستمهای انتقال را افزایش دهد.
تولید لوله فولادی؛ آیندهای پایدار برای صنایع
تولید لوله فولادی به دلیل ویژگیهای منحصر به فردی چون مقاومت بالا، قابلیت تحمل فشار و عمر طولانی، به عنوان یکی از ستونهای اساسی صنایع مختلف شناخته میشود. از صنایع نفت و گاز گرفته تا ساخت و ساز و حتی پروژههای زیستمحیطی، لولههای فولادی به دلیل تنوع در انواع و پوششهای محافظتی، گزینهای ایدهآل محسوب میشوند. طبق گزارشهای بینالمللی، رشد سالانه تولید لولههای فولادی به طور متوسط 5 درصد بوده که نشاندهنده افزایش تقاضا در سطح جهانی است. در این راستا، استفاده از فناوریهای نوین و بهینهسازی فرآیند تولید میتواند نقشی کلیدی در کاهش هزینهها و افزایش بهرهوری ایفا کند. به همین دلیل، آشنایی با استانداردها و تکنیکهای مدرن تولید، نه تنها به ارتقاء کیفیت محصول کمک میکند بلکه زمینهساز توسعه پایدار در این صنعت خواهد بود. در نهایت، انتخاب صحیح لولههای فولادی و آگاهی از فرآیند تولید آنها میتواند به بهینهسازی هزینهها و افزایش عمر مفید پروژهها منجر شود.